Fostering Safer Factories: Employee Protection Tips In The Manufacturing Industry
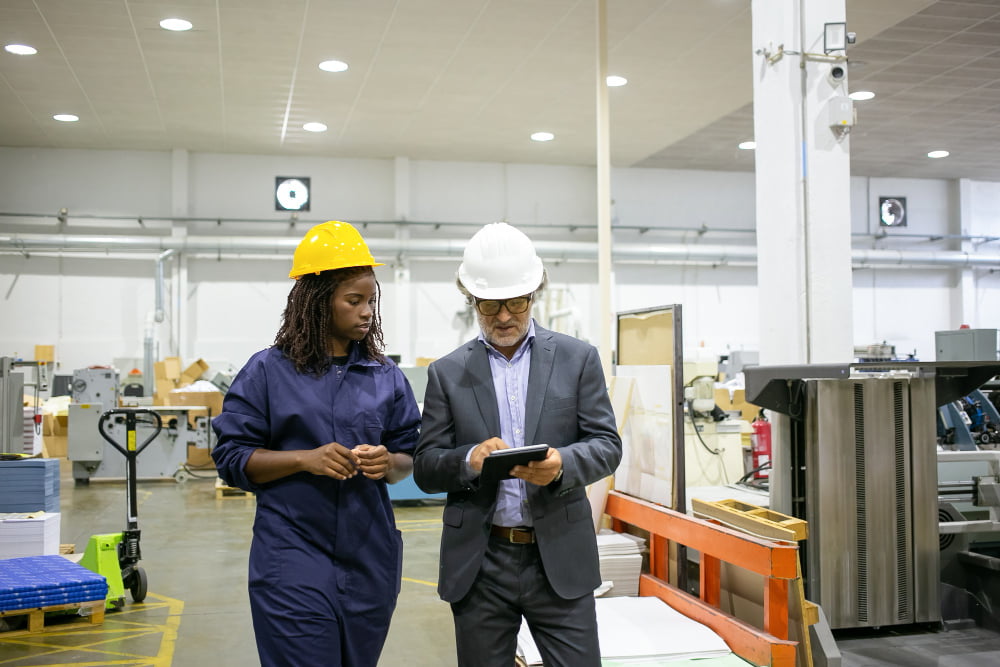
As an employer in the manufacturing industry, safety is both a moral responsibility and a necessity for success. If you want to get the best and brightest people working in your facilities, you have to demonstrate that you care about your workers. There’s no way to do that without first preventing all the worst hazards of your industry. The following tips will help you keep those hazards to a minimum and safeguard your workers for the long haul:
Obtain Essential Equipment
Industrial workplaces host a wide variety of dangers that the human body can’t weather on its own. You need to make sure that your workers have all the equipment they need to keep themselves safe from these risks. The specific equipment depends on your workplace, but in general, you should have:
- Protective Eyewear– Any employee working with chemicals, swinging objects, light, radiation, or small chips of metal, wood, and other materials needs to wear protective eyewear. Make sure what that the eyewear is suited to their specific activity and that they’re wearing it consistently and correctly. If employees wear glasses or contact lenses, you need to either use eyewear they can wear over these visual aids or eyewear that aids their vision on its own.
- Hard Hats– Any employee working underneath heavy objects or near electrical equipment needs to wear a hard hat. Hard hats are divided into A, B, and C classes. C hats provide protection from impacts but not from electricity; A hats offer limited protection from electricity; and B hats protect employees from as much as 20,000 volts. Pick the hard hat that most closely matches your needs.
- Other Essentials– If you’re working with heavy, sharp, hot, or slippery objects, your workers need footwear that both protects their feet and offers traction. Likewise, your workers will need protective gloves and armwear, especially if they’re using abrasive chemicals or molten materials.
Equipment will protect your workers from all the ordinary hazards of their jobs. You can then address extraordinary hazards when you:
Keep the Space Clear
In the event of a fire, chemical spill, or other dangerous accident, you and your employees will have to evacuate your workplace in short order. You can only do this safely if there isn’t anything blocking the entrances and exits. To eliminate such obstacles, organize your equipment and inventory and store it out of the way. Not only does this make it easier to get out, but it lowers the chance that anyone will be injured while evacuating.
Encourage Communication
You can keep workplace emergencies to a minimum if you address them in their earliest stages. Clear communication increases your chance of learning about them early enough to address them. Encourage your staff to inform you of anything dangerous or unusual they notice, even if they aren’t sure it matters. The more information you have, the easier it is for you to be proactive about safety, resolving problems before they get out of hand.
For more information on taking a comprehensive, proactive approach to workplace safety, contact F.A.S.T. today.